主軸のトルクと出力,回転数の関係(相互変換機能あり)
工作機械の主軸を選定するときや,加工条件を決定するときに,主軸のトルク線図(出力線図,トルク出力線図)を参考にすると思います.
これについて思ったことをまとめておきます.
まず利便性のために,トルクと出力,回転数の相互計算表を以下に示します.
既知の2項目に数値を記入し,未知の1項目の計算ボタンを押せば,計算結果が表示されます.
計算内容については,それより下に示す文章を参照してください.
項目 | 数値入力部 | 計算実行 |
---|---|---|
トルク(N·m) | ||
出力(kW) | ||
回転数(rpm) |
まず,トルクと出力,回転数には次式の関係性があります.
\( P = \cfrac{2 \pi T S}{60 \times 1000} \approx \cfrac{TS}{9549} \)
\( P \): 出力 (kW)
\( T \): トルク (N・m)
\( S \): 回転数 (rpm)
式中に回転数が入っているので,回転数によって,トルクや出力が変化することになります.
ここからは,グラフ上で具体的にどのような変化を示すのかを確認します.
まずは,出力線図を眺めている状況を仮定して,トルクを100Nmの一定値としたときの出力の変化を下図に示します.
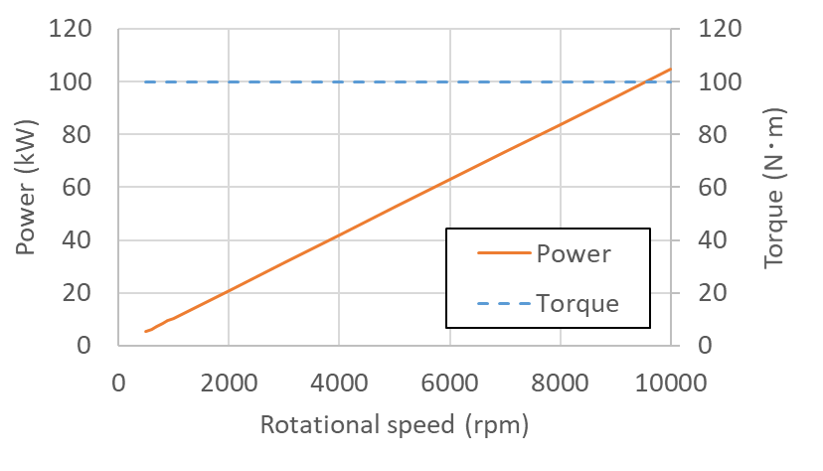
図 トルク100N・mのときの回転数と出力の関係
上式で示した関係性のとおり,回転数の上昇に伴って出力が線形的に上がることがわかります.
次に,トルクの一定値を100N・m,200N・m,300N・mと変化させたときの出力の変化を下図に示します.
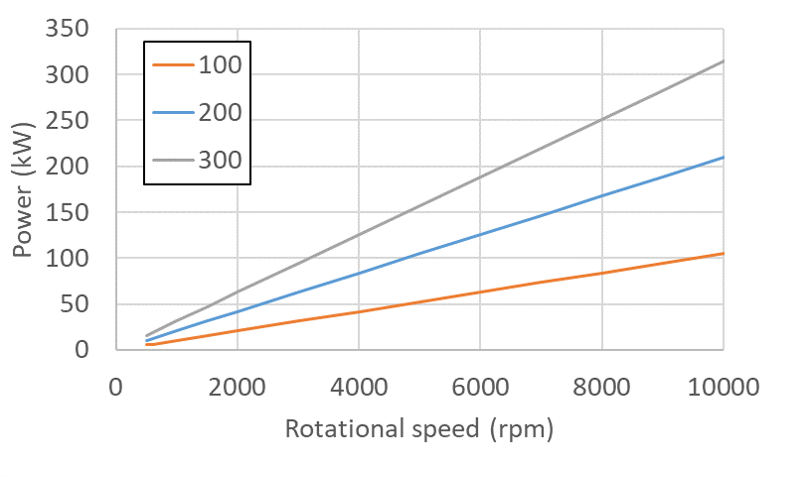
図 トルク100N・m,200N・m,300N・mのときの回転数と出力の関係
このときは,原点を通る直線の傾きの変化が生じることがわかります.
次に,トルク線図を眺めている状況を仮定します. 上式を式変形して,トルク基準の形に書き直しておきます.
\( T = \cfrac{60 \times 1000 \times P}{2 \pi S} \approx \cfrac{9549P}{S} \)
出力を100kWの一定値としたときのトルクの変化を下図に示します.
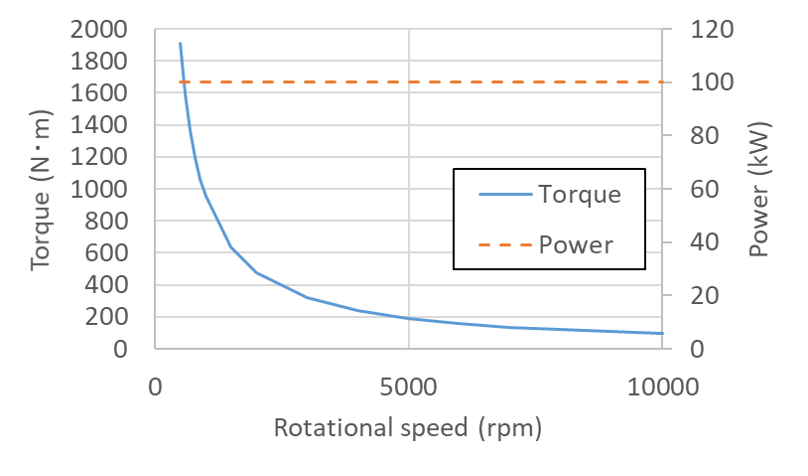
図 出力100kWのときの回転数と出力の関係
上式で示した関係性のとおり,回転数の上昇に反比例してトルクが下がることがわかります.
次に,出力の一定値を100kW,200kW,300kWと変化させたときの出力の変化を下図に示します.
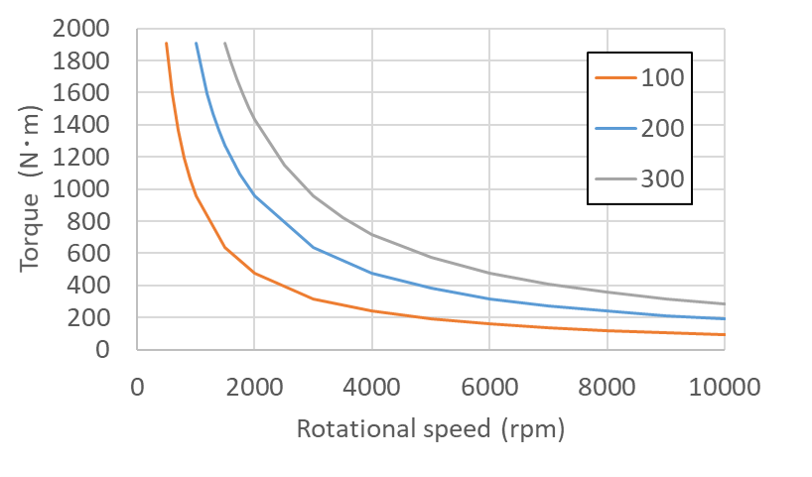
図 出力100kW,200kW,300kWのときの回転数と出力の関係
反比例の式なので,出力線図とは異なる変化を示すことがわかります.
これだけだと数式とグラフを描いただけなので,主軸の定格トルクと定格出力の参考値を使った概略図を以下に示します.
BT50,BT40,BT30,HSK63でメーカが公開している数値を適当に拾ってきて数値を丸めてグラフ化していますので,特定の工作機械の数値というわけではありません.
また,シャンクサイズ別でグラフを作っていますが,シャンクサイズでトルク線図や出力線図が決まるわけではないので,あくまで参考値です.
よって,自分が使う予定や自分が使っている工作機械で同様のグラフを作ったほうがいいと思います.
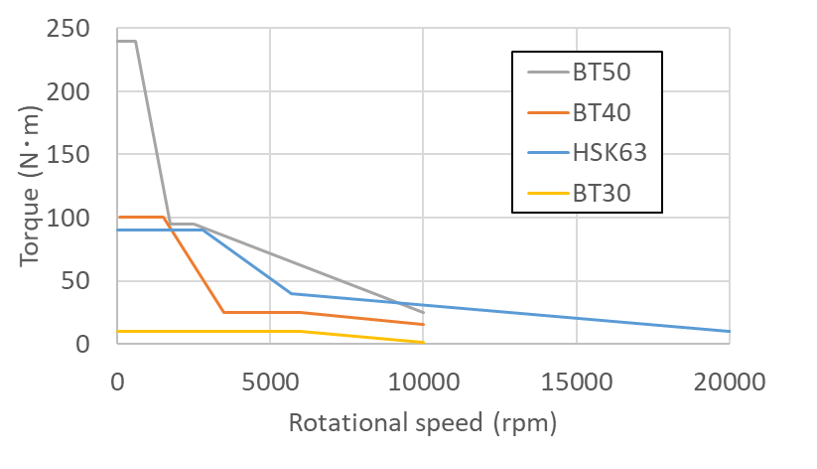
図 シャンクサイズによるトルク線図の変化
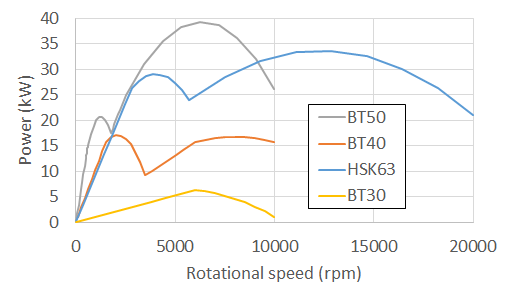
図 シャンクサイズによる出力線図の変化
このように描いてみると,シャンクサイズによって加えられるトルクが大きく異なることがわかります.
シャンクサイズが大きい工作機械で使っている加工条件を,シャンクサイズが小さい工作機械に移してもそのままでは使えないであろうことが容易に想像できます.
ここまでの話で,各線図の見方はなんとなくわかるかと思います.
あとは,これらの線図をどのように使うか,というのが重要です.
1つ目に重要な考え方は,出力が高いところを使う,ということです.
これは,出力は仕事率であり,仕事率はざっくりいえば加工能率なので,出力が高いところを使えば加工能率を高くできるからです.
次式に,フライス加工の所要動力(切削動力)を示します.
\( P = \cfrac{ a_{p} \times a_{e} \times V_{f} \times K_{c}}{ 60 \times 10^6 \times \eta} \)
\( a_{p} \): 軸方向切込み深さ (mm)
\( a_{e} \): 半径方向切込み深さ (mm)
\( V_{f} \): 1分間当たりのテーブル送り速度 (mm/min)
\( K_{c} \): 比切削抵抗 (MPa)
\( \eta \): 機械効率係数
次式に,加工能率を示します.
\( M_{rr} = a_{p} \times a_{e} \times V_{f} \)
\( M_{rr} \): 材料除去能率 (mm3/min)
これらの2式を組み合わせると次式が得られます.
\( P = \cfrac{ M_{rr} \times K_{c}}{ 60 \times 10^6 \times \eta} \)
これにより,出力と加工能率に線形的な関係性があることがわかります.
では,出力が高いところを使えばそれだけでいいのか,ということになるのですが,そうではないと考えます.
上式中には,比切削抵抗\( K_{c} \)が含まれています.
比切削抵抗は,1刃当たりの送り量と,刃先形状による寸法効果の影響を受けます.
ざっくりとした関係としては,1刃当たりの送り量を大きくすれば,比切削抵抗\( K_{c} \)が小さくなるという関係です.
つまり,同じ材料除去能率\( M_{rr} \)である切削条件であっても,1刃当たりの送り量が大きいほうが,出力が小さくなるということです.
ここでいう1刃当たりの送り量は,実1刃当たりの送り量なので,半径方向切込み深さや軸方向切込み深さの影響も受けます.
これが2つ目に重要な考え方であると考えます.
切削条件の設定には大きく分けて,高切込み低送りと,低切込み高送りの2種類があると思います.
低切込み高送りは,この効果を狙っていて,限界まで加工能率を高めるための切削条件設定方法なのかもしれないと思いました.
トップページに戻る
切削加工解析用の計算ページへのリンクに戻る